In the beginning came the drill press, which gave us 1-axis machining.
The lathe gave us two axes. The knee mill gave us three.
These days, machine tools are advertised with as many as eleven axes, but 3- and 5-axis machining are the most common. But what are these axes and how do they apply to modern machine tools?
What are the Axes in 5-Axis?
We all know the story about Newton and the apple, but there’s a similarly apocryphal story about the mathematician and philosopher, Rene Descartes.
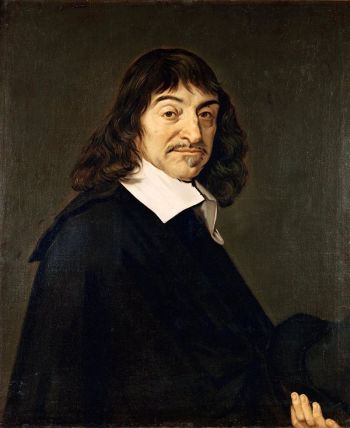
Rene Descartes. (1569-1650)
This is the Cartesian Coordinate system, and it’s still in use more than three centuries after Descartes’ death. So X, Y and Z cover three of the five axes in 5-axis machining.
What about the other two?
Imagine zooming in on Descartes’ fly in mid-flight. Instead of only describing its position as a point in three-dimensional space, we can describe its orientation. As it turns, picture the fly rolling in the same way a plane banks. Its roll is described by the fourth axis, A: the rotational axis around X.
Continuing the plane simile, the fly’s pitch is described by the by the fifth axis, B: the rotational axis around Y.
Astute readers will no doubt infer the existence of a sixth axis, C, which rotates about the Z-axis. This is the fly’s yaw in our example.
If you’re having difficulty visualizing the six axes described above, here’s a diagram from Hurco North America:
One last note about axis-labelling conventions: in a vertical machining center, the X- and Y-axes reside in the horizontal plane while the Z-axis resides in the vertical. In a horizontal machining center, the Z-axis and Y-axis are reversed. See the diagram below: