Technology that automates any age-old industry is bound to be met with skepticism from its practitioners. With machining, it is the machinists that have to be convinced that some new process will really save time through automation. They are too often subjected to the incurable optimism of technologists.
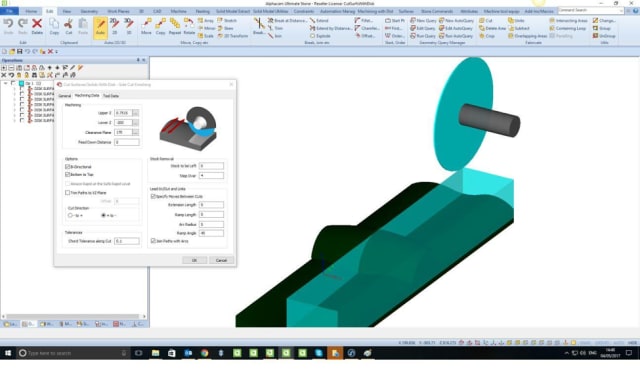
The latest release of Alphacam from Vero Software continues on the technologists mission to automate crucial CAD/CAM operations.
Machine shops and job shops are always looking for faster ways to machine components, parts and assemblies and maintain a very high level of quality. If they are a machine shop that uses Alphacam, then learning about new features and implementing them could improve productivity and profit margins.
The Automation Manager
This digital wunderkind has more support for other 3D file formats and allows users easier Multi-drill control and Styles functionality.
Advanced Automation Supports Processing
Constrained Drawings, Parametric Sketches and Part Grain Direction are processed automatically through sheet Grain Direction and Alignment Vector options.
Transferring Toolpaths to RoboDK’s Offline Programming (OLP)
This feature allows Toolpaths generated from Alphacam to be used for robotic kinematic simulation and to simulate other operations, such as robot milling, after being sent to RoboDK, which then outputs them to the robot controller.
Integrated Microsoft Analytics for Software Data Collection
Incorporating Microsoft Analytics to collect software usage data for feedback and prototyping software is useful for gathering data and making incremental yet impactful changes.
The benefits of adding Microsoft Analytics Platform System include having a parallel processing integrated system to analyze hybrid warehouse data.
New Features in The Stone Module
New in the Stone Module is support for automatic detection of unsawn areas of the selected parts and option to add a Water Jet Cut Path operation—with two extra tabs for Dialog for the Water Jet Cut Parameters and Lead In/Out settings.
The Input CAD Extensions add-on now supports all imported file types. New news as well for the dialog according to Alphacam Brand Manager Simon Mathhias, who says that “the dialog will only be displayed if the CAD file imported something that can be processed – for example, at least one instance of geometry, text or spline. Otherwise the dialog won’t be shown.”
Common Line Removal Option
This feature allows you to clean up the geometry of imported CAD file formats (there are now more available and compatible 3D file formats as well), which automates CAD import which may come in handy during batch processing through the Automation Manager. This will probably work well in file formats such as DWG and DXF, where designed layers that may overlap are unnecessary for manufacturing on a CNC machine.
The supposed benefits of automation can come at the price of familiarity. Ultimately, CAD/CAM software designers are beholden to machinists who use their products. If they work, they generally receive praise, and if they hinder and add pressure to deadlines, then they can at least communicate directly with companies like Vero Software and register their opinions, comments and suggestions. User feedback is incredibly important to CAM companies, as is the reception of criticism from hardworking CNC machinists.
Machine shops who use Alphacam 2017 will find a few new features that could help speed all that machining up a little bit.
Every little bit helps.