Pick and place, sorting, and packaging applications often require high speed manipulation of low-mass objects, especially in the electronics and food industries. Delta and SCARA robots are both designed for these applications. For many manufacturers looking to set up automation, the question is: which robot architecture is best?
To help answer that question, I spoke to experts from Yaskawa Motoman, OMRON, Kawasaki Robotics and FANUC.
To read more specifically about delta robots, check out my article The What, Why and How of Delta Robots.
Both types of robots are typically used high speed material handling. Due to the high inertia and the design of the two types of robots, payload is limited. However, the speed capabilities of these two types of robots is no joke.
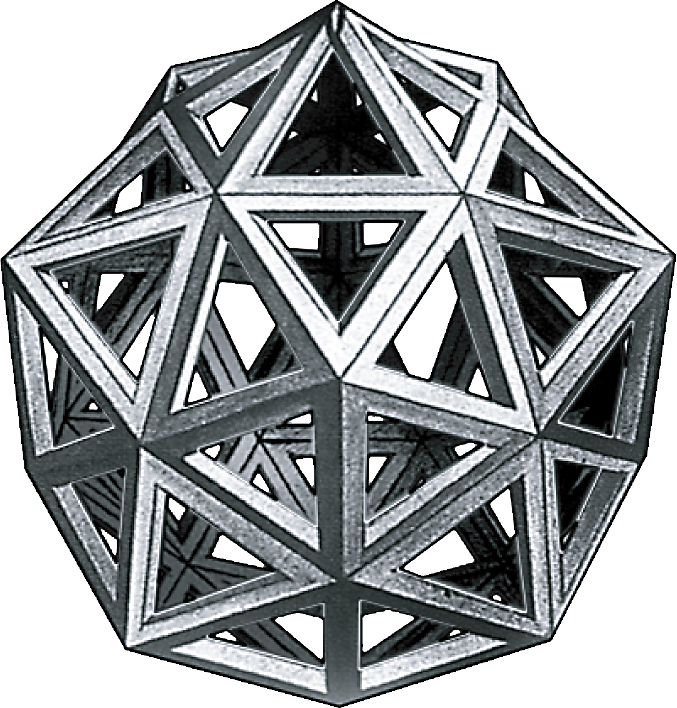
The OMRON Adept Quattro, a unique four-armed delta robot, is capable of a maximum speed of 10 m/s, with a payload of 6- 15 kg, depending on the model. The workspace is a cylinder measuring 1300 mm in diameter and 500 mm high. The Quattro boasts a pick rate of 300 picks per minute. The pick rate of the FANUC M-2iA, another delta robot, comes in at 182 picks per minute. However, SCARA robots have other advantages which make this decision more nuanced than you may think.
Payload
“Largely, 80 percent of the time or greater, for the application of a delta you’re looking at three kilograms or less,” said Dean Elkins, segment leader for material handling at Yaskawa Motoman.
SCARA robots, on the other hand, are generally more robust. FANUC, for example, offers two SCARA models at 3kg and 6kg, respectively. Epson offers the G20, which has a 20kg payload. Yamaha offers large SCARA robots with payloads up to 50kg. As with all serial manipulator-type robots, the payload is chiefly limited by the size and power of the motors.
Speed
I touched on speed briefly above, but to dive into the application-specific speed differences, let’s turn it over to the experts.
“A typical application for these types of robots could be doing things that are more akin to kitting, or changing part orientation for blister packing or some of those types of high-speed movements,” said Elkins. “If you’re looking at bringing product into a work shell in a very straight line if you will, with some variance about the length of a mat top conveyor, delta robots are very good for that type of application. If you had to have a more cylindrical work envelope for the application—for example, if you were going to be transferring products from a ball feeder, or doing some assembly process where you had to move parts from a more radial-type cell, that perhaps is where SCARA robots would hold an advantage. But, if you’re just doing high speed picking and maybe moving from one conveyor on the left to a conveyor on the right and you’re doing very linear moves for that transfer, that’s where delta robots shine.”
According to Atef Massoud, automation engineering manager at Omron Automation, the design and structure of the robots is a major contributing factor to their performance. “SCARA has, of course, different kinematics than the delta,” said Massoud. “Delta is unique in the fact that the motors are stationary. However, in the articulated SCARA, each joint carries the other motors. As a result, the delta can move at a much faster speed because it’s not carrying its own motors.”
However, Massoud agreed that the work envelope is the key differentiating factor. “In terms of work envelope, the SCARA is more suitable for some tasks more than others. It can do pick and place, but it’s more suitable for assembly or something that you need a deeper stroke. The delta are very suitable for high speed pick and place for light objects.”
For another comparison, Samir Patel, director of product and advanced engineering at Kawasaki Robotics, compared the two robots with cartesian coordinate robot systems, a popular inexpensive option. “SCARA comes between delta and cartesian in speed. The fact that the arms are somewhat more robust compared to delta robots, they are a bit heavier and a little bit limited in speed compared to deltas. They are fast, but compared to delta robots, they are slower.”
Cost of Delta vs. SCARA Robots
“In terms of cost, I would say delta robots are in the middle,” said Elkins. “With SCARA robots, when you get down to 200 millimeters of reach, those tend to be quite inexpensive in construction and design. Delta robots are typically an 850 millimeter or 1,300-millimeter design with a larger casting on the top of it, and the motors are a bit larger to move those arms and get the torque that you need. So those tend to be a little bit more expensive. Cartesian machines can be actually a little bit more than delta robots at times.”
IP Rating
“The good thing about SCARA is because you have jointed axes, you can enclose them and get as high as IP67, just like deltas,” said Patel. “Both our robots are offered up to IP67 rating. Food grade oils can also be used in gearboxes to meet certain standards. With cartesian, it is difficult to enclose all the bearings and guides to achieve a high IP rating.”
Accuracy and Repeatability
In electronics assembly and other high-precision applications, the repeatability of automation is a key deciding factor. As a rule, the need for repeatability limits the capacity for speed. This is because the arm needs time to come to rest at each pose, and after moving its mass at high velocity, vibration takes time to dissipate. This increases with payload and reach, as well. Delta robots are not as accurate as SCARA robots. For example, the Kawasaki YF03N, a 3kg-payload delta robot, features a repeatability of +-0.1mm. The FANUC SR-3iA, a 3kg-payload SCARA robot, features repeatability of 0.01mm. “Of course, cartesian robots are inherently very accurate,” said Patel. “All the control system has to do is move in xyz. There’s not much mathematics that goes into the kinematics, so cartesian robots are excellent for accuracy.”
Assembly Applications
So, for high-speed pick and place applications, delta could be the best option. On the other hand, for precise tasks at a lower cost, SCARA shines. Let’s take a closer look at assembly applications.
“SCARA can be suitable for applying force for assembly or inspection but it’s a different envelope, and the speed range is not as high,” said Massoud. Phil Zanotti, product manager at FANUC America agreed. “One thing that deltas may struggle with are insertion applications, where there’s a lot of force required,” said Zanotti. “That’s where you maybe look at SCARA or serial arm instead.”
Elkins summed it up this way: “I think the biggest comparison is that you always have to weigh speed versus Z stroke, as well as in some cases accuracy or repeatability, depending on how you’re programming the robot. Cartesian robots are typically slower, but they afford you a little bit more Z stroke. So, a cartesian robot is going to be very well suited for an application like case packing, for example. I think the deltas and the SCARA robots would be upstream of that type of application.”
Installation
With gantry-style cartesian robots, of course, the traditional method is to move in cartesian coordinates. It’s a probably cheaper solution, but will occupy a lot more space, and may require more time to set up and integrate,” said Massoud. “So, it’s not a pre-assembled robot like the delta or the SCARA. But for some applications with very heavy loads or very repetitive motion, cartesian might be a suitable solution.”
“One challenge with the delta is you need a pretty sturdy overhead structure,” said Patel. “The inertias at high speed are so high, that you need a very rigid structure over the workspace. There is a large volume under the robot which can be accessed, which is a benefit. “SCARA can be wall, floor or ceiling mounted. Plus, the form factor could interfere when they are placed right over the conveyor. They have a cylindrical workspace, but they are not as open around themselves.”
Because of the overhead structure required, SCARA robots may be more suited to more flexible deployments where the robot will be relocated in a shorter timeframe. The SCARA robot is the most compact and self-contained option of the three.
Conclusion: Delta or SCARA?
Like all questions in the field of industrial robotics, the answer is dependent on your specific needs. Every automation deployment is almost unique, and it’s useless to say one is better than the other without the context of your scenario. Your local distributor or system integrator can help you find the best solution for your application.
However, with insights from experts from Yaskawa Motoman, Kawasaki Robotics, FANUC, and OMRON, we’ve taken a look at the benefits and strengths of each type.
Where to Use a Delta
Delta robots excel at conveyor-tracking tasks, typically using vision systems to pick and place parts, or perform kitting, packing or basic, low-force assembly tasks. They require a large space to set up and require guarding due to their high speed and acceleration. Delta robots are generally more expensive than comparable SCARA robots, but thanks to their higher pick rate, one delta can in some cases manage the throughput that would otherwise require two SCARA robots, for example. Delta robots naturally have 3 degrees of freedom, and additional axes are added at the central platform, adding cost. Both types of robots can be outfitted for clean room or food-safe operations due to their enclosed designs.
Where to Use a SCARA
SCARA robots typically have four degrees of freedom, as the z plane can also rotate on a theta axis. SCARAs are generally cheaper, more compact and more easily redeployable than delta robots. They are also capable of applying more force in the z-axis, such as for insertion, fastening or assembly tasks.
If you’re researching robots for your first automation project, check out my article, How to Pick, Pitch and Purchase Your First Industrial Robot.
For more on delta robots, check out The What, Why and How of Delta Robots.