VL 1 Twin Line is a new gear hobbing solution released by EMAG which features a twin spindle design, allowing it to work on two transmission components at a time, including production of planetary and sun gears, cams, and more. The technology aims to reduce cycle times while maintaining performance quality amid rising market demands.
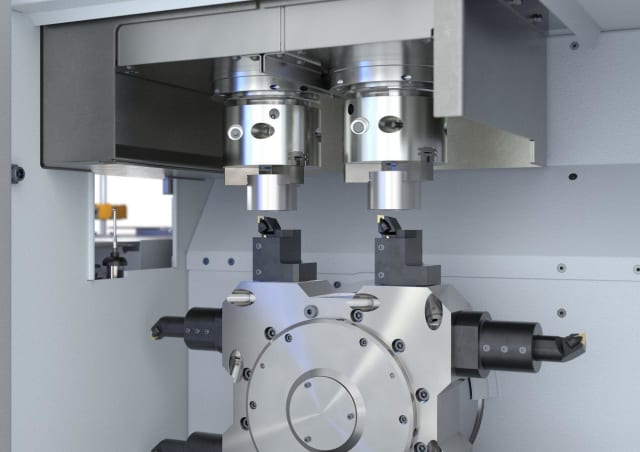
With the automotive industry growing and innovating faster and faster, manufacturers are posed with the challenge of meeting increasingly complex demands. Increasing number of gears in transmissions means an increase in the quantity of components produced. This means maintaining, or even improving, the standard of quality while meeting the power density requirements of modern transmissions. Additionally, they must also meet expected performance features, such as long service life with optimal dynamic response.
It was EMAG’s goal to reconcile the two, accelerating production while still achieving performance-accurate outputs through the VL 1 Twin Line.
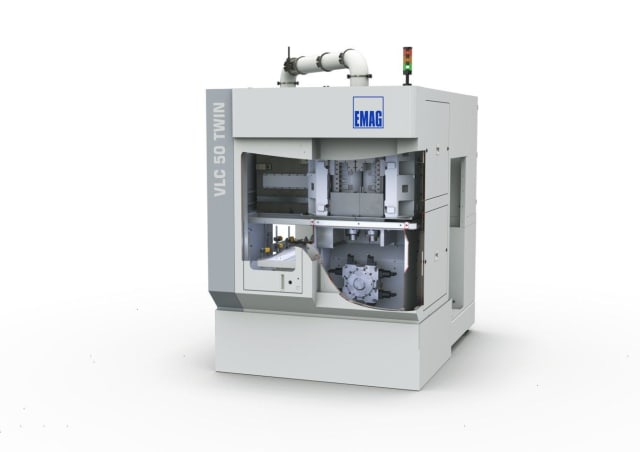
“We have developed a low-cost machine that enables high output volumes with short lead times due to its two pick-up spindles and also ensures dynamics as well as repeatability and long-term accuracy with its direct distance measuring systems in the X-axis, size 45 recirculating roller guide rails, and innovative linear motor. It is a solution for turned parts with diameters of up to 75 millimeters (3 inches),” says EMAG President and CEO, Peter Loeztner.
The VL 1 Twin Line uses a “productive twin approach” which the company claims can drastically minimize cycle times. The twin spindle design means two identical components can be produced simultaneously. According to EMAG, cycle times can be reduced to as much as 20 seconds or less. This allows for lower unit costs for the soft machining of planetary gears.
The machine is powered by a TrackMotion automation system. This is what allows the machines to work on both sides of two components simultaneously in OP10 and OP20. The TrackMotion system has a maximum travel speed of 150 m/min (5,905 in/min), allowing for quick fulfillment between operations. The VL 1 Twin Line is also equipped with an extensive parts storage area for raw and finished parts.
Additionally, innovative technology was used to increase process reliability. The linear motor in the x-axis is paired with a precise distance measuring system, which can be configured between the machining area and the pick-up stations. Recirculating roller guides ensure rigidity while the polymer concrete base of the machine reduces vibrations throughout the turning process.
For more information on the VL 1 Twin Line, visit EMAG’s website here.
For more similar stories, check out how the Automotive Additive Manufacturing Market to Reach $5.3 Billion by 2023 here.