In the field of composite 3D printing, Markforged is highlighted as a pioneer, given the 2014 release of its continuous carbon fiber printing system. And while many other firms are slowly filling the space with their own unique processes for 3D printing with composites, there may be no other more direct competitor than Anisoprint.
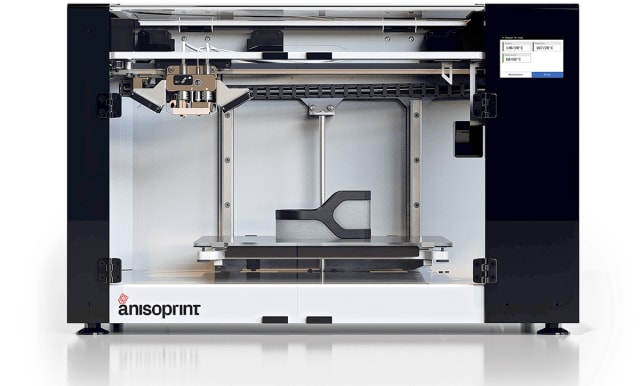
The Russia- and Luxembourg-based startup first introduced a similar, yet quite different method for 3D printing carbon fiber in 2014. In the past year in particular, Anisoprint has made a series of announcements demonstrating that it may be ready to take on the competition. To learn more, we spoke to its CEO, Fedor Antonov.
How Composites Are Made
To understand Anisoprint’s composite 3D printing process, it’s useful to differentiate the three varieties of composite manufacturing techniques that are currently used. Composites are made up of a reinforcement fiber, such as carbon or glass fiber, and a matrix material, such as a polymer.
One approach to making parts that are reinforced with a fiber material involves using a reinforcement fiber pre-impregnated with a polymer matrix, resulting in what the industry calls a “prepreg.” This stock, preformed material—usually a weaved fabric—can then be used for a variety of applications, such as forming an autobody part for a racecar.
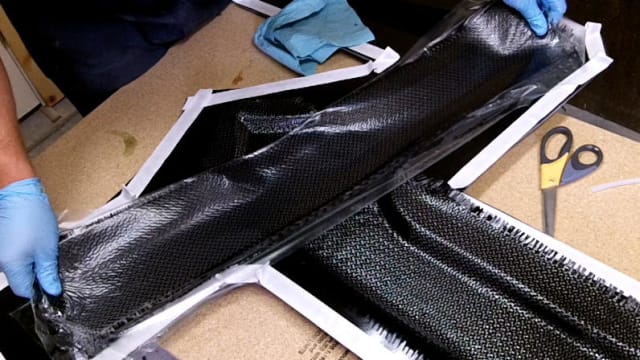
If a part is not made with a prepreg, the reinforcement fiber can be impregnated as an element of the part itself. For instance, a carbon fiber cloth might be placed into a mold in the shape of the final component, before the mold is filled with an epoxy and cured.
Finally, the third option, is that the fiber is simultaneously impregnated with the matrix material at the same time that the form of the part is being made.
Whereas the prepreg approach results in a great deal of control over the quality of the material, it is limited in terms of the final form that the part can be made from, as the prepreg must fit into or be modified to fit into the desired shape. The second approach allows for greater flexibility of the final form, but the material quality is usually lower than what is found in prepregs.
Here it’s worth noting that in pretty much all fiber composite manufacturing, individual fibers are laid out in one direction before a second layer of fibers is laid out in the opposite direction. This is because the fibers only exhibit their desired physical characteristics along the grain. If a part is to exhibit those properties in all directions (a feature known as “isotropy”), additional layers with different fiber orientations must be used to compensate. The concept of isotropy is crucial to the advantages of Anisoprint’s technology and will be discussed in greater detail further down.
What Is Composite Fiber Co-Extrusion?
Markforged’s continuous filament fabrication process actually relies on the prepreg approach. Carbon fiber is pre-impregnated with the thermoplastic nylon. With only one input and one output, the printer itself has a single channel from which the fiber is extruded.
In the case of Anisoprint’s composite fiber coextrusion (CFC) technique, there are two inputs and one output; one input is dedicated to the reinforcement fiber and the other is dedicated to extruding thermoplastic. How this works is that, rather than using a reinforcement material pre-impregnated with thermoplastic, which is very viscous in its liquid state, Anisoprint pre-impregnates the dry fiber with extremely liquid thermoset resin that is then cured into a solid state. This virtually eliminates the odds of introducing air bubbles and voids into the material.
The thermoset prepreg fiber is then extruded together with a traditional desktop 3D printing filament made from thermoplastic. The thermoset matrix within the reinforcement material can then bond well with the thermoplastic filament.
The Benefits of CFC
What this means is that CFC is not necessarily limited in terms of the plastics that can be extruded and merged with the reinforcement fibers. Recently, Anisoprint partnered with Chinese filament manufacturer Polymaker to create profiles of 3D printing filaments that can be used in conjunction with Anisoprint’s reinforcement materials. This includes PETG, ABS, PC, PLA and PA.
As for reinforcement materials, Anisoprint currently offers a carbon fiber and basalt. The firm’s carbon fiber composite is 20 times stiffer and stronger than traditional plastic with strength and stiffness-to-weight ratios that are five times greater than 2024-T351 aluminum, while remaining seven times lighter and stronger than steel.
Basalt offers similar properties to fiberglass and is a cheaper alternative to carbon fiber, in that it is 15 times stiffer and stronger than traditional plastic, five times lighter than steel, and features a strength-to-weight ratio twice that of 2024-T351 aluminum. It is also nonconductive.
In addition to using a wider material set, CFC can actually control the rate of deposition of said plastic. As a result, some very unique structures and properties can be achieved. In particular, CFC is capable of printing lattice structures, something otherwise impossible in traditional composite manufacturing.
This is in part due to the fact that when fiber-reinforced elements cross over one another in a component, that area doubles in thickness. However, because CFC can control the flow of the thermoplastic as it is printing, it can reduce plastic deposition substantially as elements overlap.
3D Printing Carbon Fiber Lattices
The importance of such an achievement is hard to grasp without a deeper familiarity with composites. In composites, the more fiber reinforcement material there is in relation to the total volume of the composite (known as the material’s “fiber volume ratio,” or “fiber volume fraction”), the better the mechanical properties that are exhibited, in most cases.
“We can locally apply more or less plastic and if we apply more plastic, there will be a lower fiber volume fraction. If we apply less plastic, we can get a higher fiber volume fraction,” Antonov explained.
With carbon fiber 3D printing, the ratio is typically stuck around the 30 to 40 percent range. However, in the aerospace industry, engineers typically look for fiber volume ratios of up to 60 percent, according to Antonov. Though CFC can achieve ratios of up to 45 percent, the ability to create lattice structures can actually double the fiber volume fraction at the junctions where fibers cross over one another.
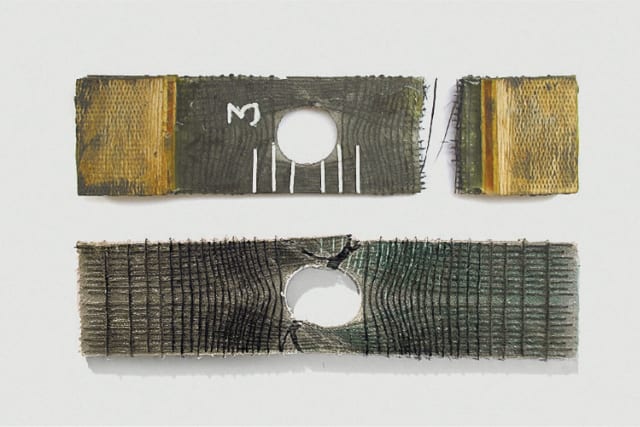
In other words, 3D-printed lattice structures made up of carbon fiber and other composite materials have the potential to be even stronger than forms made with traditional composite manufacturing technologies. At the same time, such structures can be made without all of the additional weight and material associated with composites made from woven carbon fiber fabric.
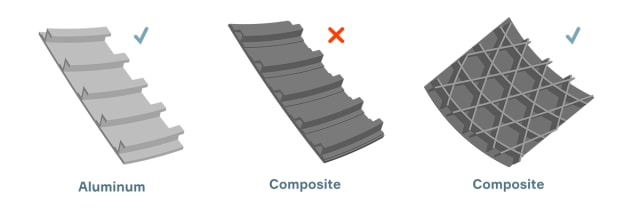
As discussed earlier, manufacturers that rely on composite parts often attempt to mimic isotropy through the use of multiple layers of unidirectional fibers. The result is all-over strength with excess material density. Antonov explained that, ideally, it would be possible to place only the necessary material and strength where it is needed, making it feasible to reduce the material and weight of the part where that strength is not needed.
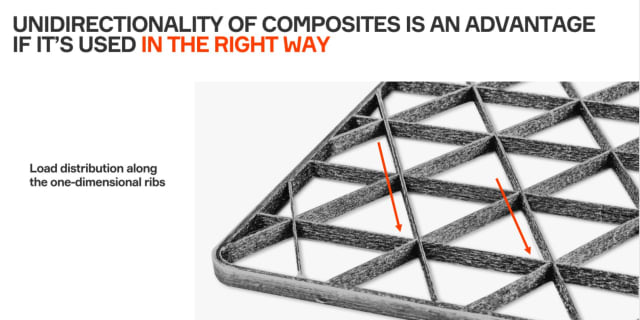
“Every part has certain loading conditions, certain internal forces, and the goal of an engineer is to align the material properties along these forces to optimize the physical properties of the part—and to not have excessive properties in the direction they’re not needed,” Antonov said.
Antonov pointed out that, in nature, many durable structures, such as fly wings and leaves, are actually anisotropic, sparing material where necessary while maintaining shapes that don’t bend in response to the forces of gravity and wind. “Anistropy is an advantage in composite materials. That’s why we’re called Anisoprint,” he added.
Inventing Composite Fiber Coextrusion
Anisoprint was born out of research being conducted by Antonov at the Skolkovo Institute of Science and Technology (Skoltech) in Moscow. After obtaining a degree in fundamental mechanics and a PhD in mechanics of formal solids at Moscow State University, Antonov worked at Skoltech to establish the Center for Composite Materials.
“We had a team made up of members from all over Russia who were experts in the design optimization of composites. We had a common idea on how composite materials should be designed, but there was no technology able to actually produce those designs physically,” Antonov said. “So, we decided to come up with the hardware and the material technology to allow us to manufacture these designs we were working on theoretically.”
The first experimental trials began in May 2014, resulting in a working process by the end of the year. As fate would have it, by May 2015, Skoltech decided to rework the center, dropping the financing for the team’s research. That decision, however, spurred Antonov to spin the work out of the university and form Anisoprint.
Unlike some of the more marketing-heavy startups based in the U.S.—which are sometimes able to garner significant funding from venture capital before products have even proven themselves‚ Anisoprint initially struggled to get off the ground. It took the company about a year and a half to obtain its first customer and two years to obtain its first round of funding from an angel investor.
It wasn’t until early 2017 that product development could even begin, followed by the first production batch by 2018. By November of 2019, customers were buying systems and, from that point on, Anisoprint had hit the ground running.
Antonov attributes the slow start to the fact that his team, including himself, was initially made up entirely of scientists who were content with working in university labs and focusing on research. It wasn’t until Skoltech essentially bumped them from their nest that they learned to fly into the market.
Now that he has become comfortable in an executive leadership role, Antonov says that he is no longer involved in the science of composite 3D printing. However, there is the possibility that a more business-minded individual will step in to become CEO, while Antonov moves on to a more technical position where he can focus on what he loves most.
“One day, I still hope I will have a chance to have more time and focus to go a bit deeper into the technology side of the business because that’s still something I feel more confident in, but the current situation requires me to stay on in this role right now,” he said.
Those who have been following the 3D printing industry for some time will recognize that Markforged is a powerhouse when it comes both to product development and financial backing. It was identified early on as an innovative player in the space, allowing it to receive significant investments from venture capitalists so that now, not only does the company offer fiber reinforcement 3D printers, but a metal 3D printing technology as well.
According to Antonov, this is actually a good thing. Markforged is helping to prep the wider manufacturing market for composite 3D printing technology, a phenomenon that Anisoprint can actually take advantage of.
“About half of our customers already have Markforged machines. And they bought them because there was no alternative, but they were not really sold on [Markforged] completely. With our offer, we can address more needs that they can’t satisfy with our product,” Antonov said.
As Anisoprint continues to develop its own product offering, it will also seek investment in order to stay ahead of the market.To learn more about the company, visit the Anisoprint website.