As much of North America braces for the harsh winter climate, many drivers substitute their traditional road tires for snow-friendly ones. Like gasoline, which has summer and winter-weather blends, winter tires use a different formula more suitable for cold temperatures. The science behind cold weather tire performance is complex, and their design requires a higher level of engineering than traditional tires. The novelty of cold-weather tires is how the rubber chemistry relates to the physics of how they interact with the road. With the unique rubber chemistry, the design of snow tires also leverages different principles of physics that promote winter driving performance.
Rubber Chemistry
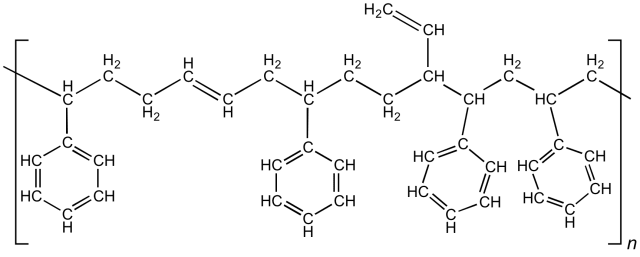
Conventional automotive tires use a unique blend of formulated rubber. A machine accepts the constituents of the rubber and automatically blends the recipe to make the desired blend for the tire. The chemistry of tire rubber is complex, and engineers have developed and optimized the process over many years. The primary raw materials used in tire manufacturing and their uses are:
- Natural rubber - cis-1,4 polyisoprene (C5H8)n is an organic compound that exhibits stretchy properties from weak C-H bonds. It is collected as latex from rubber trees and refined into rubber. Sensitive to both temperature and atmospheric oxidation, engineers often vulcanize natural rubber to crosslink the polymer chains
- Synthetic rubber - formulators make styrene-butadiene rubber by thermally cracking naphtha from petroleum. More chemically consistent than the natural material, synthetic rubber augments the raw material taken from rubber trees to provide the base for the tire material.
- Sulfur - a critical component in rubber vulcanization, formulators mix sulfur with rubber and heat to between 140-160°C to form crosslinks between isoprene polymers. Natural rubber has low intermolecular strength, and the vulcanization process improves the rubber’s resistance to oxidation and reduces its thermal sensitivity.
- Carbon black - used to optimize handling, reduce friction wear and hysteresis, and improve abrasion resistance, carbon black is a powder form of carbon that reinforces the tire rubber. It also offers UV resistance to prevent tire rot.
Key Additive: Silica
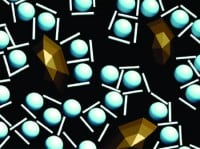
This image from Toyo Tires illustrates the dispersion of the Silica in the compound
Toyo Tires has optimized the dispersion of silica in its winter tires rubber to promote the flexibility of the tread blocks. This flexibility is the property that allows the tire to maintain grip with the road.
Design and Physics
One of the most significant differences in the physics of winter tires vs. all-season is the tread. Typically, winter tires have wider, deeper grooves that dig into the snow to improve traction. This benefit translates into winter tires exhibiting a coefficient of friction that is nearly double that of all-season tires, thus cutting the required stopping distance in half through the definition of kinetic energy. Goodyear’s Ultragrip series has been leading winter tread geometry design for years. These grooves do add noise and bumpiness to the driving experience due to the wider, deeper tread depths. Michelin has been optimizing its winter tires to reduce these factors.
Though the treads are the most apparent difference, the rubber chemistry is starkly different. Engineers design all-season tires to improve performance in warmer months, softening as the temperature rises and adhering to small imperfections on driving surfaces. As the temperature falls, though, all-season rubber hardens, decreasing the friction coefficient with the road. Winter tires, employ a softer rubber compound than all-season tires. The sweet spot for this rubber is under 40°F, making them ideal for cold months. This feature drastically reduces tread wear on winter tires in warm months, so they are not suitable for year-round use.
Winter tires also have “biting edges,” which, as the name suggests, increases the contact area between the tire and the driving surface. These zig-zag shaped grooves cover the tread and help the vehicle adhere to the ice or snow-covered road. Firestone incorporates this feature its Blizzak winter tire design.
Key Design Feature: Sipes
Sipes improve traction and cornerning performance. (Image courtesy of Toyo Tires.)
Takeaway
One of the most important (and misunderstood) components of winter tires is that they are not only for snowy surfaces. The chemistry of the winter rubber formula is ideal for sub-40°F temperatures, not precipitation conditions. With each product development cycle, the design and chemistry of winter tires continue to improve. Engineers are designing winter tires that decrease stopping distance and grip the road better than ever. They also aim to deliver a winter driving experience with the smooth, low-noise performance of all-season tires. The high degree of engineering in both the rubber chemistry and design features explains why winter tires are a must-have as the temperature drops.