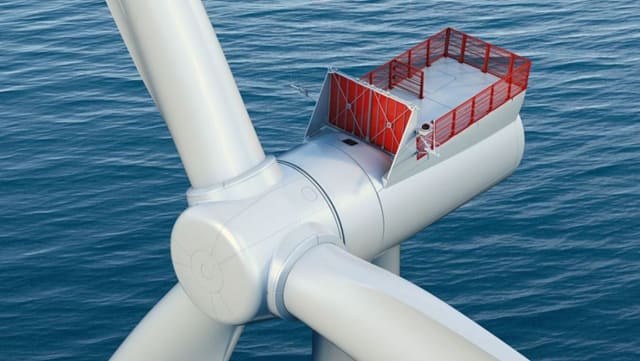
Wind energy generated by wind turbine technology is one of the fastest developing sustainable power sources due to its promising potential. Two types of wind turbines share the focus of current development efforts, and are competing to be recognized as the dominant design: the gearbox, and the direct-drive wind turbines. This article will examine both types of turbine, and discuss the advantages and disadvantages, as well as tackle their potential to become the dominant type of wind turbines in the market.
Gearbox Wind Turbine Type
There has been a shift in wind turbine technology in the last few decades, which has lead to the variable speed wind turbine with a multi-stage gearbox. This type of turbine has a gearbox between the low-speed rotor and a higher speed electrical generator (usually a relatively standard doubly-fed induction generator). The purpose of the gearbox is to increase the rotational rotor speed before feeding it to the generator.
For this wind turbine type, the blades rotate by a shaft connected via a gearbox to the generator. For example, to generate electricity in the case of a 1 MW wind turbine, the gearbox increases the rotation speed of the blades from 15 to 20 rotations per minute up to the about 1,800 rotations per minute that is required.
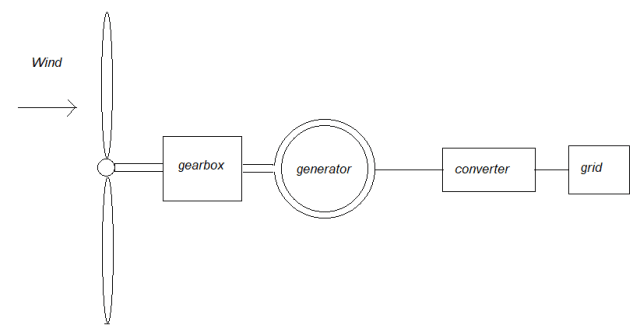
This type of wind turbine presents a challenge for designers because of the loading and environmental conditions required for the gearbox operation. The power is generated via torque from the rotor; however, large moments and forces are also applied by the turbine rotor on the wind-turbine drivetrain. To prevent stress concentration and failures, designers must adjust the gearbox to support the loads and stress. Seals and lubrication systems must operate consistently in wide temperature variations; otherwise, dirt and moisture may collect and build-up inside the gearbox.
Direct Drive Wind Turbine Type
To eliminate gearbox failure and transmission losses, manufacturers have developed wind turbines without gearboxes. This type of wind turbine was introduced in 1991, and is known as the variable speed direct-drive wind turbine. Direct-drive technology is the basis for direct-drive wind turbines; as Shown in the image below, the synchronous generator is directly powered by the rotor.
A direct-drive wind turbine’s generator speed is equivalent to the rotor speed, because the rotor is connected directly to the generator. As the rotational generator speed is low, designers placed several magnetic poles in the generator to achieve the appropriate high output frequency.
The there are two categories of wind turbine generators: permanent magnet generators (PMGs) and electrically excited synchronous generators (EESGs).
EESGs do not have permanent magnets made from rare materials, such as neodymium, the extraction of which can cause environmental damage. On the other hand, PMGs have several advantages such as high efficiency with the elimination of field loss, in addition to being small and lightweight compared to the EESGs. PMGs are usually used in small-scale wind turbines, but can also be used in large MW applications.
However, because the high torque requirements are large, direct-drive wind turbines up to 7-10 MW require significantly larger and heavier generators. In this case, a single or two-stage gearbox is the better choice, as it is a much smaller, lighter solution and it provides the same advantages as the direct-drive generator.
To produce electricity at a low rotary speed, the manufacturers had to design a specific generator. Since traditional generators have a cylindrical shape, the permanent magnet synchronous generators provide a better fit for direct-drive due to their “doughnut” configuration. However, to achieve the required high torques, the effective permanent magnet rotary motion must be increased. Ultimately, this means that a significantly larger diameter generator must be provided.
An advantage of direct-drive turbines is the high efficiency of synchronous permanent magnet generators. An important fact is that due to wind inconsistency, the turbines often operate at partial loads. The efficiency of the PM generator excels even in these conditions because it continues working nearly to nominal values.
Several benefits are added here within the advanced control features, which provide users with high energy yield, quiet operation and long-term reliability and availability. Because the direct-drive wind turbines do not have a gearbox, mechanical noise is reduced as well as fewer rotating components. Moreover, this type of wind turbine has a single main bearing for the rotor assembly and generator, which additionally reduces the number of moving parts, as well as the maintenance and repair costs.
Gearbox vs Direct Drive
When it comes to the gearbox wind turbine, the wind turbulence can cause enormous stress to the wheels and bearings in a gearbox, which can in turn lead to defects in the turbine components and ultimately stopping the mechanism. The faster the wind, the more vulnerable gearboxes are; this means that offshore turbines are more exposed than onshore ones.
The gearbox is the highest-maintenance part of a turbine; therefore, removing the gearbox improves the reliability of a turbine. The gearbox is also the heaviest element in a turbine, weight-wise, so removing it improves this aspect of a turbine, as well.
Manufacturers have been researching for years on how to increase the competitiveness of the direct-drive versus gearbox turbines. This is why the technology of the former has improved in design, both in terms of complexity and maintenance, making direct-drive turbines practical for offshore wind applications. However, the downsides of direct-drive technology—the cost and weight of the direct-drive turbines—have prevented it from presenting major competition to the gearbox turbines until recently.
The developments in direct-drive magnets and generator arrangements resulted in a more affordable, lighter direct-drive model. The price of the permanent magnets used in direct drive turbines has also dropped significantly, increasing the popularity of the direct-drive turbines.
On the other hand, there are thousands of gearbox turbines currently available and in use in the market, which means that this type of turbine can’t suddenly retire. Because of this, wind turbine manufacturers continue developing gearbox technology to reduce outages and increase its reliability. As a result, the magnetic systems of wind turbines are now lighter, and require less copper.
Key Determinants for Dominant Turbine Technology
The aspects that affect technology efficiency and determine which turbine type will become the dominant one in the market are:
· Manufacturer brand reputation and credibility;
· Technological characteristics: total energy yield, cost, and reliability;
· Price (product price and the price of service and maintenance);
· Availability of scarce materials (i.e. magnets used for permanent magnet direct drive generators);
· Manufacturer’s warranty;
· The number of suppliers for the components.
The most important factors for selecting proper wind turbines are cost and technology reliability. The cost of energy is the key factor that influences the strategic decision for building new wind farms. Ideally the price should remain fixed for a prescribed period, which would allow for insight into the technology that provides the lowest cost of energy being at an advantage over its competitors.
The second important factor is the reliability of wind turbines. Wind turbines are required to operate in various locations, from easily accessible fields to remote offshore or mountain locations. Repairs and unscheduled maintenance resulting from poor reliability can be extremely costly and time-consuming. Technologies such as smart online monitoring can increase overall reliability. [2]
Expert opinions place both technologies shoulder-to-shoulder. This can conclude in one of two ways: either both technologies will continue developing until one prevails, or both types will find sufficient users to coexist in the market.
Other experts claim that direct-drive technology will eventually become the dominant one. In making this claim, they present three arguments:
1. The costs for the offshore support structure for direct-drive wind turbines is lower due to its lighter weight.
2. Direct-drive has more potential for further improvement. Experts argue the gearbox wind turbine is almost at its maximum efficiency point, while the direct-drive turbines have more possibilities for improvement.
3. Direct drive is more efficient for future higher power rating wind because the gearbox wind turbines require extra stages of gears, leading to more gearbox losses.
In the end, the gearbox technology is not dying anytime soon. However, the rotating parts involved must improve its effectiveness and efficiency as the costs for the direct drive technology are lowering. Additionally, this will also force gearbox technology to enhance its reliability. There is also a possibility for a hybrid design combining the elements of the gearbox and direct-drive designs.
[1] Bearing Fault Detection within Wind Turbine Gearbox, Suliman Shanbr, Faris Elasha, Mohamed Elforjani, Joao Amaral Teixeira, Published in 2017 International Conference on Sensing, Diagnostics, Prognostics, and Control (SDPC) 2017
[2] Gearbox versus direct drive - opening up the black box of technology characteristics, Geerten van de Kaaa, Martijn van Ekb, Linda M. Kampa, Jafar Rezaeia a Delft University of Technology, Jaffalaan 5, 2628BX, Delft, Netherlands b Croonwolter&dros, Marten Meesweg 25, 3068AV, Rotterdam, Netherlands.