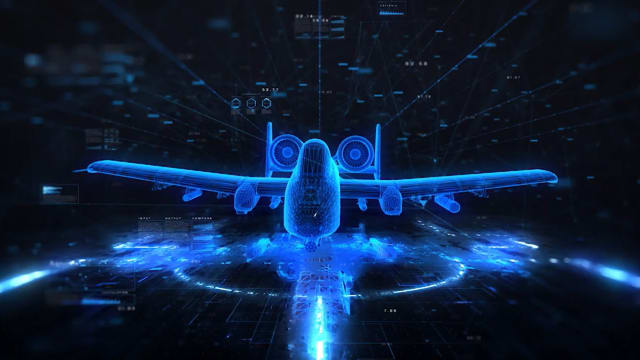
From air taxis to electric airplanes to autonomous fighter drones, the sky is rich with innovation. We spoke with Dale Tutt, VP of Aerospace and Defense at Siemens Digital Industries Software, to learn how companies from legacy giants to youthful start-ups are keeping pace.
Engineering.com: How has COVID-19 affected the aerospace and defense industries?
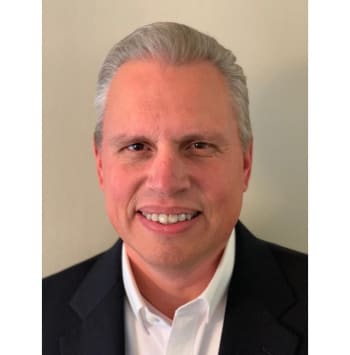
Dale Tutt, Vice President Aerospace and Defense Industry at Siemens Digital Industries Software. (Image courtesy of Dale Tutt.)
Dale Tutt: With air traffic down, it's taken a big toll on the commercial aircraft industry. Boeing and Airbus are cutting their production rates by up to 40 percent. They're expecting these reduced rates to be flat at least through next year and then to maybe start turning back in 2022-2023. It's going to take three or four years to recover back to current production levels.
This has been impactful for a lot of the supply base for a couple of reasons. One, if production rates get cut in half by 50 percent, then the amount of product to supply is cut by 50 percent, as well. However, the issue that is not as obvious to a lot of people is that there are a lot of companies that rely on maintenance, repair and overhaul—the product support. That is driven more by hours on the airplane and number of landings. If you're a supplier that refurbishes landing gears or brake systems, then if you're not landing airplanes, you're not putting cycles on brakes—and so your maintenance business goes significantly down as well.
The defense side is a little bit more stable. I think they are projecting 2 or 3 percent declines over the next couple of years, but for the most part, these defense programs are funded. They are going to be fairly stable.
What is Siemens doing for aerospace and defense?
We can cover the entire life cycle of a product, from the smallest part to the largest part. The breadth of our product solutions cover things like model-based systems engineering early in the design process, moving into some of the design and analysis tools that you use during the engineering process. As you move into manufacturing, we help companies ramp up the production rates faster and be more flexible to changes. Changes are inevitable as you go through the development of an aircraft or defense product.
The lifecycle of airplanes is 60 years. You spend 10 years developing it and spend 50 years supporting it. The fact that we're able to provide this breadth of solutions across the entire product life cycle helps companies make that transition from engineering to manufacturing. The more seamless you can make that transition, the easier it is for the manufacturing team to be more flexible and more agile. It is the same thing when you go into product support. We can really partner with the company across the entire digital transformation and across the entire product cycle.
What simulation tools are available for aerospace and defense?
A lot of our analysis and CAD tools are used for stress analysis, but we also have a lot of 1D and 3D simulation tools that can look at how the system performs. We have CFD analysis that goes into the aerodynamics of the airplane. We're able to provide the solution sets across what we call the virtual integrated aircraft and be able to fly it before we build it. As you're developing a new product, whether it's a landing gear system or an entire airplane, the ability to understand how it's going to work in an integrated simulation can really reduce a lot of your risk.
If you can identify changes before you start building, it helps you to be much more effective with your test programs. When you're developing a test program, you can take the flight envelope and you can spread the points equally across the entire flight envelope. However, if you can effectively use simulation, you can identify areas of no concern, and areas that are more critical, because you have better information. You're able to focus your energy on those test flights, so you have a much more effective test program. Not only are you cutting out all the unnecessary changes that might happen during a flight test or ground test program, but you're also being much more efficient with the use of your test assets.
On the product support side, we have a lot of tools in place to transition from “as designed” to “as built” to “as maintained.” We're finding with some of our customers that a lot of the simulation tools we use during manufacturing also apply to preparing for service. You want to do a more efficient job of service. If you're bringing an airplane in for a large maintenance overhaul, you have to take pieces of the airplane off, you have to work on it, and you have to bring it back together. You need to know that it’s all going to fit together.
How do you optimize that? How do you optimize the flow of parts to the airplane? How do you optimize all of the tools that you need to maintain an airplane? If you're doing a major upgrade, you can plan that all with the same tools.
Is the industry embracing digitalization?
There's no doubt in my mind that they are seeing digitalization as an advantage. They look to us as a partner to help lead them there, because it's not easy. If you think about the spectrum of digitization, on the one end you have digital twins. People have been doing digital twins with a CAD model or simulation model, but we've been able to extend that much further now with digitalization, where you're starting to connect it.
We often think of the twin as the “What.” What are you designing? What are you building? The thread is the “How.” It's the context, the connectivity. When you have a requirement you can trace to a verification plan, to the design, to how it's being manufactured, to how it’s being supported, you have this continuous thread that's traced all the way back to the original set of requirements. Sometimes requirements change, and you're now going to do a very good impact assessment of what all the downstream functions are that are affected by that requirement change. You have a lot better information to make your decisions with.
When you get to that ideal state of having the full digital twin with full connectivity between all of your different processes, then you start to see productivity enhancements. Due to the automation, you start to see more innovation because people are actually able to spend more time focusing on solving those problems.
Companies see the value of digitalization. It’s a question of how to get there. How long have we been talking about paperless systems, and how long did it take for us to actually achieve paperless systems? It takes time, but we're able to partner with companies to help them with that, to take them down that path and to be able to connect to some of their legacy tools.
We see companies that are doing this today, and they're seeing truly transformational results. Companies that are using Xcelerator are seeing 30 or 40 percent improvements in their development cycles. All of a sudden, you take a year off of your development cycle—that's real money. We're seeing a lot of success with our customers in making that transition to full digital transformation.
What exciting innovations do you see in the industry?
I think air taxis are just a matter of time. There's still a lot of demand for the whole concept of air taxis over these big urban environments. Instead of being stuck in traffic on the 405 out in Los Angeles, you're able to fly over it in an air taxi in a much cleaner fashion, because you're using electric propulsion and you're not just sitting there in traffic. I think it's super exciting. I saw a stat last year, there's something like 200 companies working on air taxis.
It's big companies like Bell and it's a lot of little start-ups like Kitty Hawk. Kitty Hawk is a customer, they're using our software for manufacturing and for certification. It's just amazing what some of these companies are doing, and they're making great progress. They have dreamers and they're not burdened by preconceived notions. They have a mission, and they're going to go figure out how to do the mission. They don't have a bunch of people saying, "It can't be done."
As for electric airplanes, the power density of jet fuel is so much greater than the batteries right now. Still, we've seen a lot of improvements in battery technology in general. Bye Aerospace, they're a customer of ours as well, are doing fantastic work. They're fully digitized with their electric airplane and they're going through the certification process now. As battery technology has matured, a lot of companies are getting to the right point of how long we can fly.
Initially, commercial electric planes might be hybrid electric. Then as battery technology starts to improve, you start to replace fuel cells with battery cells. I think that you're starting to see the progress being made towards making that happen. You have companies like Rolls Royce, and all the other big engine companies, that are now working on electric propulsion and being very public about it.
One of the challenges with an electric aircraft is thermal. You're generating all this heat that's got to go somewhere. You have all this electrical wiring and electrical heat. We have a lot of tools, and we work with a lot of these companies on thermal management. The fact that the tools are getting strong enough now to really help these companies move faster is also going to help accelerate things. But the reality is, with all the challenges, it might be ten years before you start to see electric planes. I'd be stunned if it's any longer than that.
Autonomous combat drones, I think they're calling it a loyal wingman, is an idea that's been around for at least 10 years. The whole concept of linking, say, three drones together with an airplane is really the next level up, because there's a much higher level of autonomy. These are not so much remotely piloted as they are a little bit more remotely directed. You task them to go circle an area and now they can be doing reconnaissance, or they can be carrying weapons.
A lot of the solutions that we provide today are the same solutions that would be used to design any other airplane. Whether CAD, electrical systems design, composites design or additive, you name it, all of those technologies are the same. But when we think about these drones in a fighter squadron, it's a systems problem—not just taking the cockpit off an airplane and replacing it with an unmanned section. From a systems to systems standpoint, it’s the ability to flow down those requirements from that top-level set of requirements to the squadron to what are the types of airplanes, the types of training, the types of simulators that the pilots have to use.
It's a pretty big design problem, and we have systems engineering solutions to manage that system. We've got the system modeling and the requirements composition, and then managing that on our digital threads to be able to use that information to design, build and sustain those airplanes.
I think ten years from now, the face of mobility is completely different all around. Exciting times. And we have a lot of solutions we talked about today, and we’ve partnered with companies that are able to go faster and be much more effective in what they're doing.
To learn more about Siemens Xcelerator portfolio, visit Siemens Digital Industries Software.