For more on this, read: Part 2.
What does the optimal PLM system look like?
We will examine the answer to this question through a two-article series discussing Aerospace & Defense manufacturer Saab Aeronautics. The company is primarily known for the development and manufacture of the multi-role fighter jet JAS-39 Gripen, and for its partnership with Boeing for the development of the U.S. Air Force T-7 Red Hawk training jet, as well as the early warning radar system Global Eye.
Part 1 focuses on how Saab Aeronautics is working with existing PLM systems in the development of the Gripen aircraft.
Part 2 will examine Saab Aeronautics’ path into the future and the demands on its new PLM solution, through a discussion with the company’s leading PLM architects, Johan Tingström and technical fellow, Erik Herzog. They share their views on the possibility of the Open Services for Lifecycle Collaboration (OSLC) format as one possible base for that platform. We will also discuss a new suggested architecture, Genesis PLM, and the related solution proposal being tested in the Heliple project.
The Hunt for the Ultimate PLM System
Striving to create an optimal PLM solution isn’t a new issue; rather, it is an objective that has always engaged those tasked with creating “law and order” in the management of ever-increasing volumes of complex data. But the problems and requirements do not stop there. The situation has been further complicated by explosive technology development, often linked to changing business models and conditions.
The important question is: How do you reconcile these old systems, not only with other existing systems, but also with the new systems coming over the horizon of future technologies and changing business structures?
For those who develop aircraft, this is a daunting task—just ask Saab Aeronautics’ Erik Herzog, technical fellow in the systems engineering area, or Johan Tingström, enterprise architect. Aeronautics is a business division within Saab AB. They know where the challenges lie in terms of data integrity, interactivity, traceability and connections to new and expanded business models.
“There are a number of aspects here. Developments in the PLM area are rapid and often make older technology obsolete. Given that we have products that live extremely long—30, 40 or maybe even 50 years—it is not reasonable that all products should, or even can, be in the same PLM environment. We must be able to make a new choice for each new product,” Herzog says to engineering.com, when we meet for a discussion about requirements, challenges and opportunities to advance the PLM positions for Saab Aeronautics.
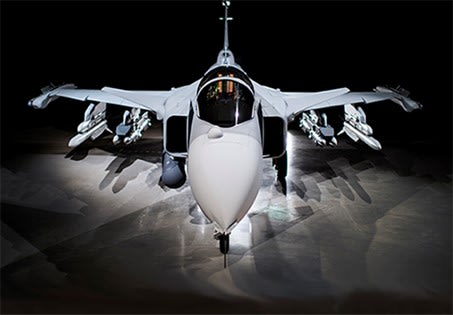
Saab’s ambitions are high, and their objective is to create what can become an ultimate PLM solution.
“We as a company have ended up in collaborative situations with varying partners,” he adds. “Sometimes we are the lead system integrator (LSI), sometimes not. This means that we must have the ability to adapt to the environment quickly and at a low cost.”
To get there, they have evaluated the solutions they already have in place, and examined what the new architecture—named Genesis—could look like. In the latter case, they have also started working on a solution proposal within the framework of the Heliple project. The focus in this context is, as mentioned above, on OSLC. What is OSLC, and how can it contribute to altering the way Saab Aeronautics operates?
To provide a broader background, I looked at how the company works today in terms of processes, where they came from and where they want to go. What are the weak spots? What software tools are they using? What do they demand from the PLM system architecture they plan to develop? How can supplier chain management be improved?
OSLC Makes It Easier to Get Tools to Work Together
OSLC is part of the OASIS Open Standards Network. OASIS itself is an international non-profit consortium that brings together companies, governments, academia and individuals to solve communication challenges. The OSLC specifications define how lifecycle applications represent, link to and access resources based on established Internet standards and linked data, including REST architecture, RDF specifications and HTTP methods. In short, OSLC makes it easier to get tools to work together and share data.
The Old Game: One Customer, One Aircraft Model
Roughly every ten to twenty years, Saab has been commissioned to develop new fighter aircraft. This paradigm has historically been one customer, one aircraft model, long development times and a few export deals. This is what Herzog calls "the old game, which we have been quite good at handling, and which has been around for a long time."
But after 2010, things began to change.
“We got a partnership between Sweden and Brazil regarding the Gripen E (2013), and a development job with a foreign customer around the early warning radar system Global Eye. However, it didn’t stop there. From Boeing we got a unique invitation to become partners in the development of the U.S. Air Force training jet, the T-7 Red Hawk. Suddenly we are in a completely new situation with multiple and parallel projects, international operations, development and production on several sites and with requirements for adaptations to varied regulations and safety regulations,” sums up Herzog.
This is a completely new and challenging situation, in which one of the important points is that it must be possible to quickly set up development environments for collaboration. At the same time, you need to offer your engineers attractive development environments. More than ten years of product development loops and the supporting IT systems were on the way to becoming obsolete, and suddenly became less than optimal in light of these new realities.
“Our life as a company has changed in this, and become much more dynamic and complicated,” says Johan Tingström. “Absolutely not a negative; on the contrary, we see it as proof that we have good international competitiveness. But what would we do to streamline product development? We had to find a solution here.”
In addition to Herzog and Tingström, I have also discussed these projects with other stakeholders in the Heliple project: Jad El-Khoury in the department of mechatronics and embedded systems at the Royal Institute of Technology (KTH), Torbjörn Holm, senior consultant and technical fellow at Eurostep, and Eurostep’s marketing director, Håkan Kårdén.
The Present Integrated Development Model
A fundamental factor in this context is that the solutions brought to the table must be in line with international "best practice solutions," states Erik Herzog.
This means having the ability to offer an optimized overall capacity, the ability to absorb the latest of the latest, to be good at adapting to new development scenarios and it cannot be too costly.
In terms of process, Saab Aeronautics is based on ISO15288, which means that the terms Saab uses are easy to derive internationally. A strong development model has also been established, which combines the stability needed to build an aircraft where the resources needed are scarce, with the ability to establish agile development work. Simply put: an overall functional architecture, in parallel with the ability to achieve long-term goals with development in small steps.
“At every development step we have to evaluate what went well and what didn’t. When we then integration-tested, typically in a fairly simple simulator, a team can deliver to a ‘warehouse’ where we then actually have all our components available. At the same time, we have an integration organization that takes ‘Lego pieces’ to assemble them into more or less complete configurations, which could go into an advanced test station or test aircraft,” Tingström sums up.
The reason for creating this iterative development model is, among other things, that what is created is so complex that ‘just-in-time’ at each development site is difficult to achieve: some teams are ready according to plan because they do not encounter any complications, while other teams are delayed due to unexpected obstacles.
“But,” Tingström adds, “we must never let those who are late influence our integration.”
CATIA in CAD, and Siemens Teamcenter as Product Data Backbone
How does Saab Aeronautics’ software arsenal look? Presently, the main tool set includes:
- Siemens Digital Industries Software's cPDm solution Teamcenter Enterprise as the backbone of product data. This system handles product structures, system structures, changes and configurations.
- The mechanical design is mainly supported by different versions of Dassault Systèmes CATIA, mainly V4 and V5, with tight integration with VPM (Dassault’s older PDM system). For a couple of specific functions, which cannot be realized in the above set, 3DEXPERIENCE is used, which is on Dassault Systèmes’ V6 platform.
- For some areas, Dassault’s V6 platform is used. Dassault originally called V6 “3DEXPERIENCE” but these days both the V5 and V6 versions are called 3DEXPERIENCE solutions.
- In terms of software development, Atlassian is the primary suite of tools.
- For system design and system-by-system simulation, IBM Rhapsody and Dassault's Modelica language-based solution Dymola are both in use, in parallel with MathWorks MATLAB and Simulink.
- DOORS from IBM is used for requirements management.
- In addition, there is a large and diverse collection of different analysis tools, both purchased and proprietary.
Engineers Jumping Between Different Front-End Environments
Overall, good results have been achieved in this environment, although there are disadvantages.
“One such [disadvantage] is that our engineers have to jump between different front-end environments," claims Herzog. “It gets a lot of back and forth due to the fact that the applications in the environments are not optimally connected to each other and also tend to age, which can be quite frustrating for our engineers. So, what's our next step? This is where we have talked a lot about the Genesis model.”
The Genesis model of thought first came into being about two years ago. Since then, a collaboration with The Royal Institute of Technology has developed in which people help to study these conditions. Among other things, a report was produced last year that points out the potential for OSLC.
This report notes that the disadvantage of Saab’s existing PLM solutions—Siemens’ Teamcenter and Dassault’s 3DEXPERIENCE—is that both create an undesirably strong dependence on a single PLM provider. The same applies if you were to choose a solution such as Syndelia (InterCAX) or Aras PLM. It’s simply important to avoid depending significantly on a single supplier.
Products That Live Longer Than PLM Systems
As can be concluded from the above, Saab Aeronautics currently has a system architecture which includes several elements of non-integrated tools. Another problem is that in the A&D industry, it is not uncommon for systems to age and risk becoming obsolete. Saab is no exception. For example, the basic installation of Teamcenter Enterprise is from 2007, which is a platform that is quite different from the same solution today, even though Saab Aeronautics has upgraded the platform over time.
The bottom line, however, is that in today's system environment, three effects in particular can be noted: many manual import and export activities, and limited traceability if, or when, proprietary interfaces cannot be used.
The conclusion here is that a new architecture for PLM support could provide a lot of benefits—but what are the conditions for a new system?
I will dive into the answer in the upcoming Part 2 article on Saab and the hunt for the ultimate PLM system.
For more on this, read: The Hunt for the Ultimate PLM System, Part 2: Saab Aeronautics and the Path into the Future.